As the global electronics industry gathers at the China Shenzhen Trade Show, Superworld Electronics is proud to present innovative solutions that are shaping the future of power management. In this ever-evolving field, engineers are tasked with designing systems that are high-performing, reliable, compact, and energy-efficient.
At our showcase, we are introducing advanced inductive components—Trans-inductor Voltage Regulator Inductors, Power Beads, and Mini Molded Inductors—that highlight the latest advancements in power management. This article will explore their technical specifications, benefits, and applications, emphasizing how these components align with current industry trends. Engineers attending the trade show will gain valuable insights to inform their design decisions and stay ahead in the competitive electronics landscape.
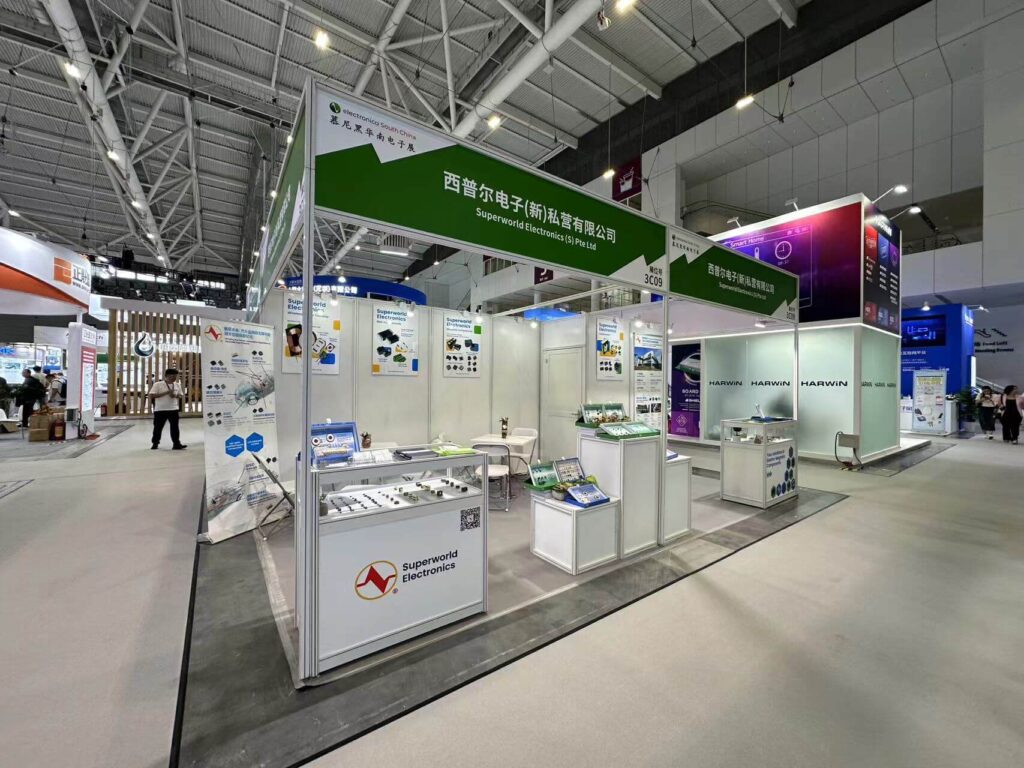
Trans-inductor Voltage Regulator Inductor
Technical Overview
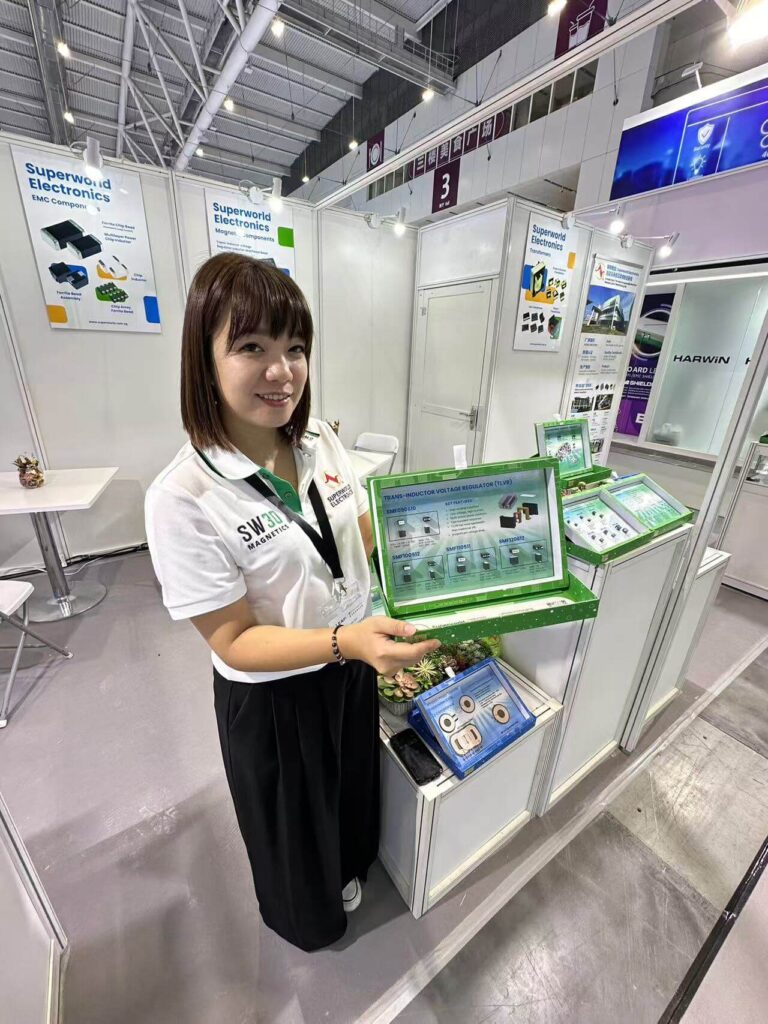
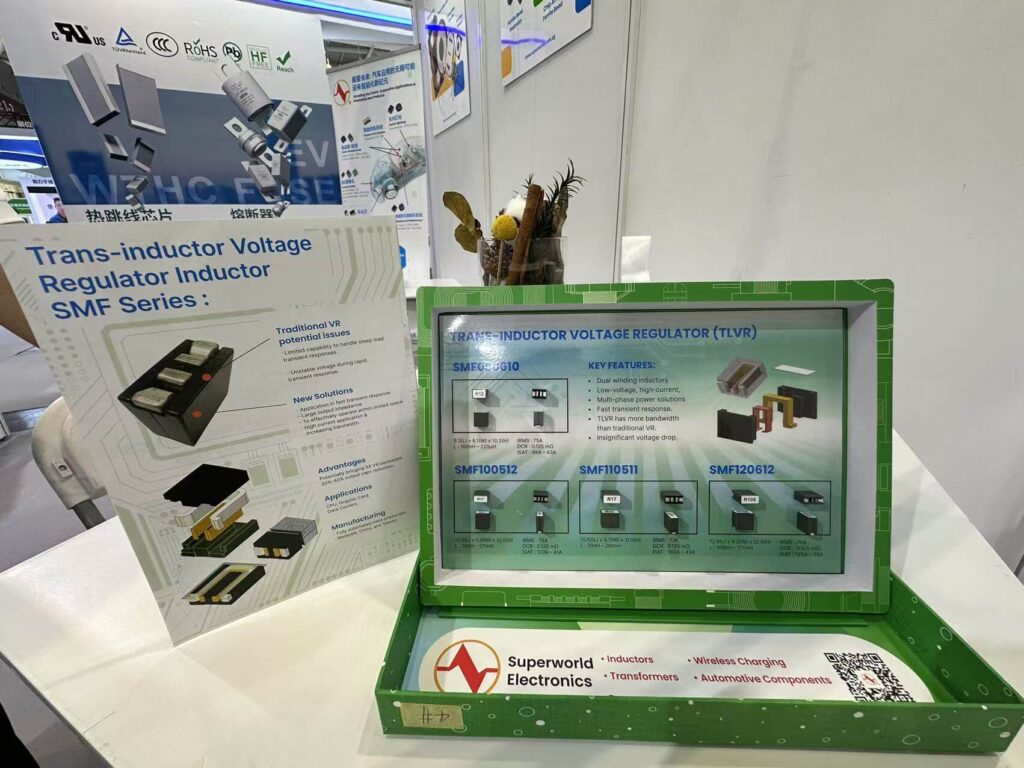
- Dual Winding Inductors:
Employs coupled inductors to enhance power efficiency and dynamic response. - Low-Voltage, High-Current:
Meets the stringent power demands of modern processors and ASICs. - Multi-Phase Power Solution:
Reduces ripple current and improves system stability through multi-phase design. - Fast Transient Response:
Quickly reacts to load changes to maintain voltage stability. - Increased Bandwidth:
Offers more bandwidth than traditional voltage regulators. - Insignificant Voltage Drop:
Optimized design minimizes voltage drop, enhancing efficiency.
Technical Benefits
- High Efficiency:
Dual winding coupled inductors reduce energy losses, improving overall efficiency. - Enhanced Dynamic Performance:
Fast transient response meets the dynamic load requirements of high-performance processors. - Space Saving:
Multi-phase design and coupled inductors reduce the number of required components, saving PCB space. - Improved Thermal Performance:
Higher efficiency and optimized current distribution reduce heat generation, aiding thermal management.
Current Trends and Relevance
- High-Performance Computing Demand:
The rise of AI and big data applications increases the performance requirements of processors. It meets these processors’ low-voltage, high-current power supply needs. - Data Center Energy Efficiency:
Data centers aim to reduce power consumption and heat generation. TLVR’s high efficiency and low-loss characteristics align with this trend. - 5G and Edge Computing:
Next-generation communication technologies require fast-responding power management. rapid transient response and high bandwidth make it suitable for these applications. - Miniaturization and Integration:
multi-phase and coupled inductor design helps reduce component count, supporting more compact system designs.
Applications
- Servers and Data Centers:
Provides high-efficiency power solutions for high-density servers. - High-Performance Computing (HPC):
Meets the stringent power requirements of supercomputers and AI processors. - Telecommunication Equipment:
Supports stable power supply for 5G base stations and network devices. - Graphics Processing:
Delivers fast, stable power supply for high-end GPUs, enhancing graphics rendering performance.
Power Beads:
Optimizing High-Current Voltage Regulation
Technical Overview
Power Bead Inductors are engineered for high-current applications, particularly in multi-phase voltage regulators. They play a pivotal role in delivering stable power to processors, memory modules, and high-current ASICs and FPGAs.
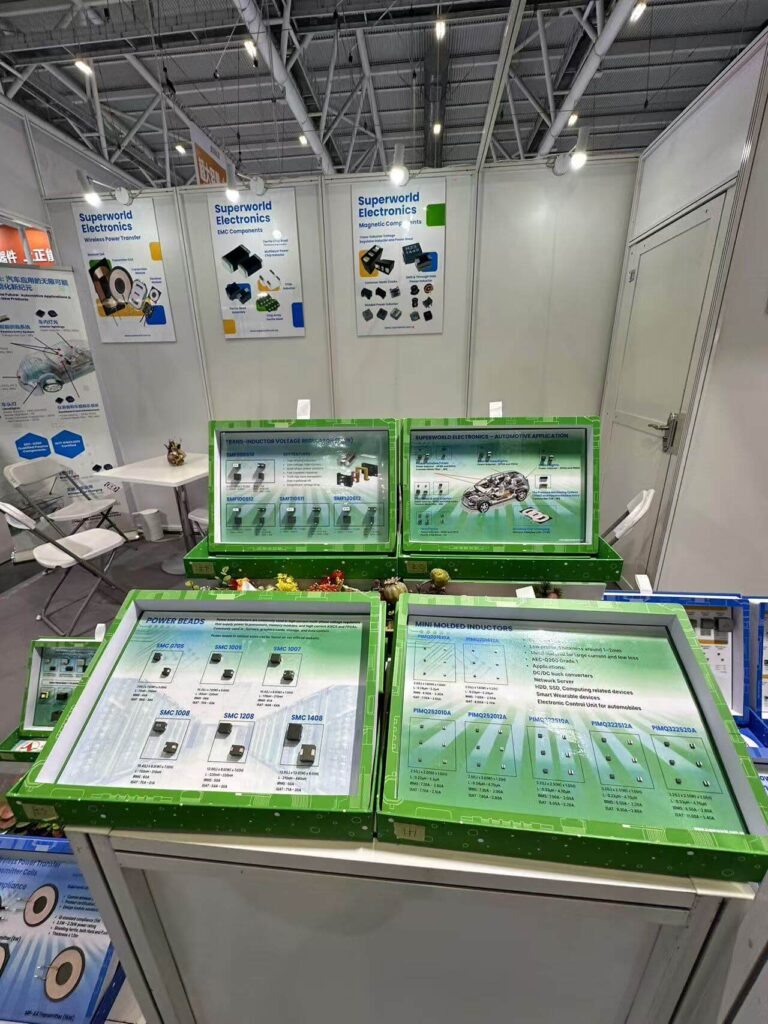
- Inductance Range:
Typically from 100 nH to 1 ÎĽH. - Current Rating:
Can handle currents up to 100 A, depending on the model. - Saturation Current:
High saturation current prevents inductance drop under heavy loads. - DC Resistance (DCR):
Low DCR minimizes power losses and heat generation. - Material Composition:
Ferrite or metal composite cores for high permeability and low losses.
Technical Benefits
- Efficient Energy Storage:
High inductance values enable efficient energy storage, critical for voltage regulation. - Thermal Management:
Optimized materials and design for heat dissipation, maintaining performance at elevated temperatures. - EMI Suppression:
Core materials and construction reduce electromagnetic interference, essential in high-frequency circuits.
Current Trends and Relevance
- Increasing Power Density:
High-performance computing and AI demand components supporting higher power densities. Power Beads are ideal due to their high current handling and compact size. - Transition to 48V Power Architectures:
To improve efficiency and reduce conduction losses, there’s a shift towards higher voltage power distribution in servers and telecom equipment. Power Beads capable of handling higher voltages are increasingly important. - GaN and SiC Devices:
The adoption of Gallium Nitride (GaN) and Silicon Carbide (SiC) devices allows for higher switching frequencies. Power Beads must perform efficiently at these frequencies, necessitating advanced materials with low core losses.
Applications
- Servers and Data Centers:
Used in Voltage Regulator Modules (VRMs) for CPUs and GPUs, ensuring stable operation in intensive computing environments. - High-Performance Computing (HPC):
Supports the power needs of supercomputers and AI processors. - Graphics Cards:
Provides consistent power delivery for GPUs, reducing voltage ripple and enhancing rendering performance. - High-Speed Storage:
Ensures reliable power in SSDs and enterprise storage solutions, enhancing data integrity and performance.
Mini Molded Inductors:
Compact Solutions for Modern Electronics
Technical Overview
Mini Molded Inductors are characterized by their compact size and low profile, with thickness ranging from 1 to 2 mm. They utilize metal composite materials to handle large currents with minimal losses.
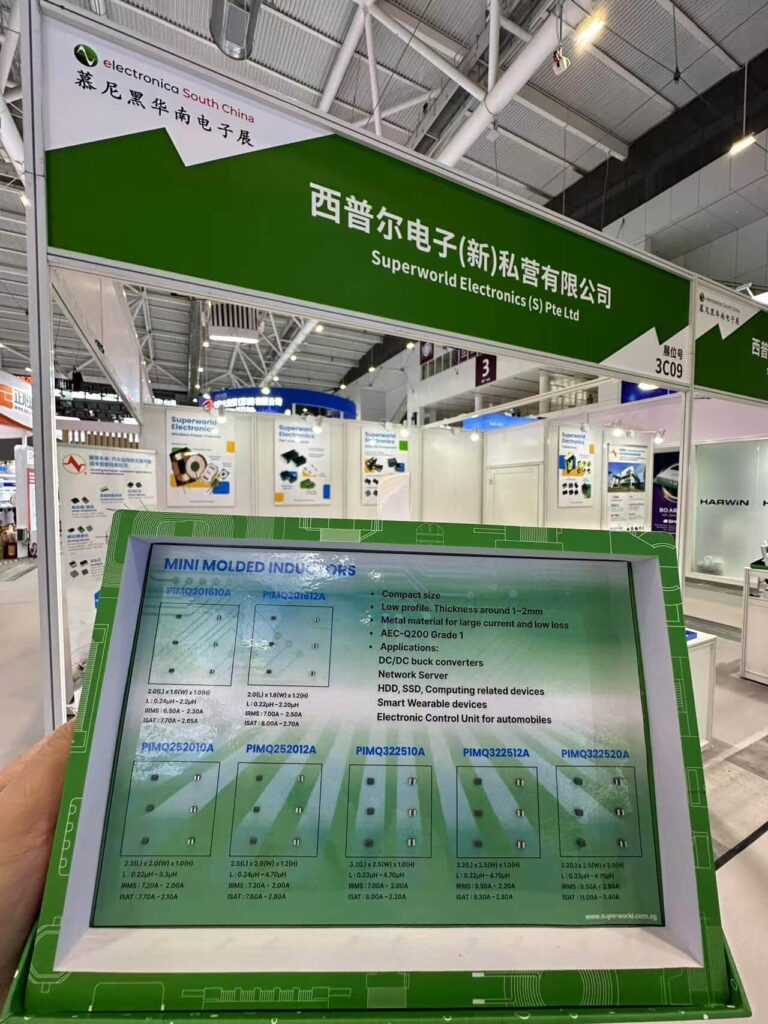
- Inductance Range:
From 0.1 ÎĽH to 10 ÎĽH. - Current Rating:
Up to 20 A, suitable for compact yet power-demanding applications. - DC Resistance:
Ultra-low DCR for high efficiency. - AEC-Q200 Grade 1 Certification:
Meets automotive industry standards for quality and reliability.
Technical Benefits
- Space Optimization:
Small footprint and low height allow for dense PCB layouts, critical in portable and wearable devices. - High Current Capability:
Metal composite cores support higher currents without saturation. - Low Core Losses:
Enhances efficiency, especially in high-frequency DC/DC converters. - Thermal Stability:
Maintains performance across a wide temperature range (-40°C to +155°C).
Current Trends and Relevance
- Miniaturization and IoT:
The proliferation of Internet of Things (IoT) devices demands components that are both small and efficient. Mini Molded Inductors meet these needs by providing high performance in a compact form factor. - Wearable Technology Growth:
Smartwatches, fitness trackers, and medical devices require ultra-compact components. The low profile of Mini Molded Inductors is ideal for these applications. - Automotive Electronics Expansion:
With the rise of Advanced Driver-Assistance Systems (ADAS) and electric vehicles (EVs), there’s a need for reliable, compact inductors that can operate in harsh environments, making AEC-Q200 Grade 1 components highly relevant.
Applications
- DC/DC Buck Converters:
Ideal for step-down voltage regulators in compact electronics. - Networking Equipment:
Used in power modules for servers, routers, and switches. - Wearable Devices:
Fits the stringent size constraints of smartwatches and fitness trackers. - Automotive Electronic Control Units (ECUs):
Ensures reliable operation in vehicle control systems, infotainment, and safety features. - Computing Devices:
Enhances performance in laptops and tablets by optimizing power management
Selection Considerations for Engineers
When choosing the appropriate inductor, engineers should consider factors influenced by current trends:
- Current and Voltage Requirements:
Match the inductor’s rating with the application’s maximum load, considering higher power densities and voltages. - Inductance Value:
Select based on desired ripple current and voltage regulation, crucial with higher switching frequencies. - Frequency of Operation:
Ensure efficient performance at the application’s switching frequency, which may be increasing due to GaN and SiC technologies. - Thermal Performance:
Consider operating temperature range and thermal dissipation capabilities, essential in high-density and automotive applications. - Size Constraints:
Evaluate physical dimensions to fit PCB layouts, particularly in miniaturized devices. - Regulatory Compliance:
AEC-Q200 certification may be required for automotive applications, aligning with vehicle electrification trends.
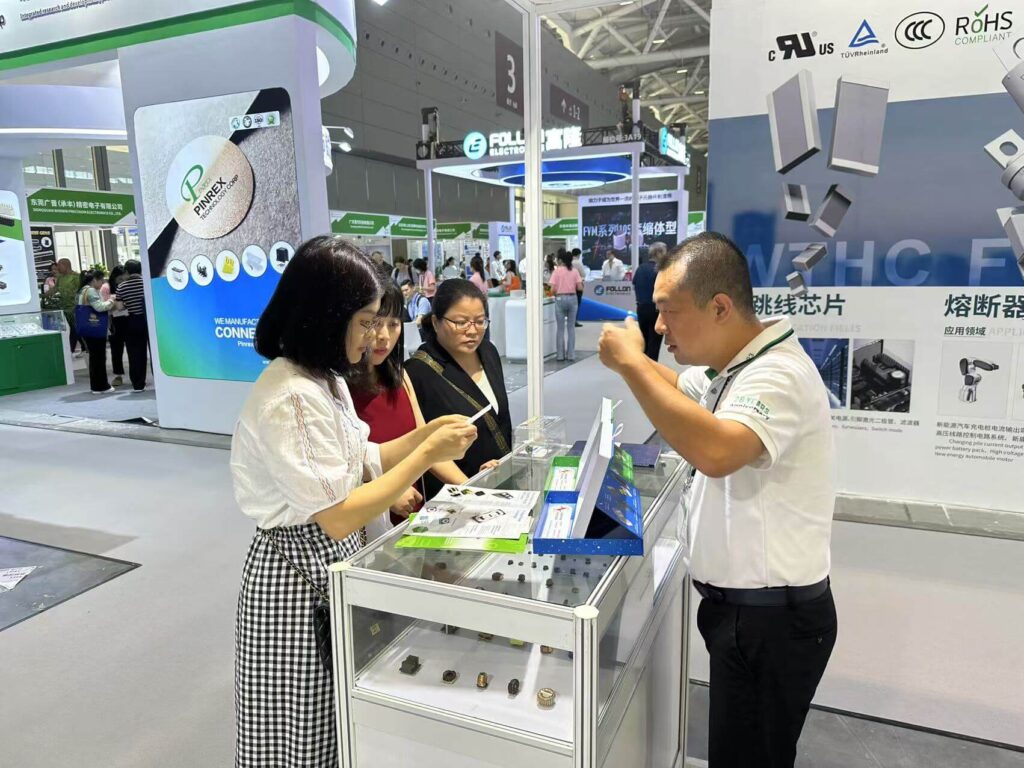
Conclusion
Trans-inductor Voltage Regulator Inductors, Power Beads, Mini Molded, are integral to modern power management solutions, addressing the challenges of increased power density, miniaturization, and efficiency. By understanding their technical capabilities and how they align with current industry trends, engineers can make informed decisions that enhance system performance and reliability.
For a comprehensive range of inductive components and technical support, visit Superworld Electronics. Our experts are ready to assist you in finding the perfect solution for your power management needs.
Follow : #SuperworldElectronics
Website : www.superworld.com.sg
Product Page : https://lnkd.in/ghdEUAqJ
Contact Us : sales@superworld.com.sg